System Integration
We integrate various system components of our clients (production lines, equipment, sensors, etc.), gather available information, and provide our clients with this data in a homogeneous and easily interpretable format. Based on individual needs, we create personalized reports and monitoring interfaces to support operational activities.
System Integration in industrial automation stands as a critical factor because integrating tools and systems is essential for efficient operation when automating industrial processes. During system integration, various systems and tools are interconnected under a single platform, simplifying overall system management.
Multiple systems can be integrated under a single platform during system integration. These may include PLCs (Programmable Logic Controllers), fundamental control units in industrial process automation, HMIs (Human-Machine Interfaces) providing the user interface, and SCADA (Supervisory Control and Data Acquisition) systems responsible for data collection and analysis.
Facilitating communication between different systems is paramount in system integration for industrial automation. Various communication protocols like Modbus, Profibus, or Ethernet are utilized to transfer data and information between systems, enabling their integration.
Security is a crucial consideration during the integration of individual systems since linking systems can pose security risks. Thus, ensuring adequate security measures such as data protection and other security protocols is vital during integration.
System integration in industrial automation simplifies overall system management, enhancing efficiency, and reducing operational costs. Moreover, it facilitates swift and straightforward transfer of data and information among systems, thereby expediting and streamlining processes.
In industrial automation, system integration aims to augment process efficiency and cost-effectiveness.
Services
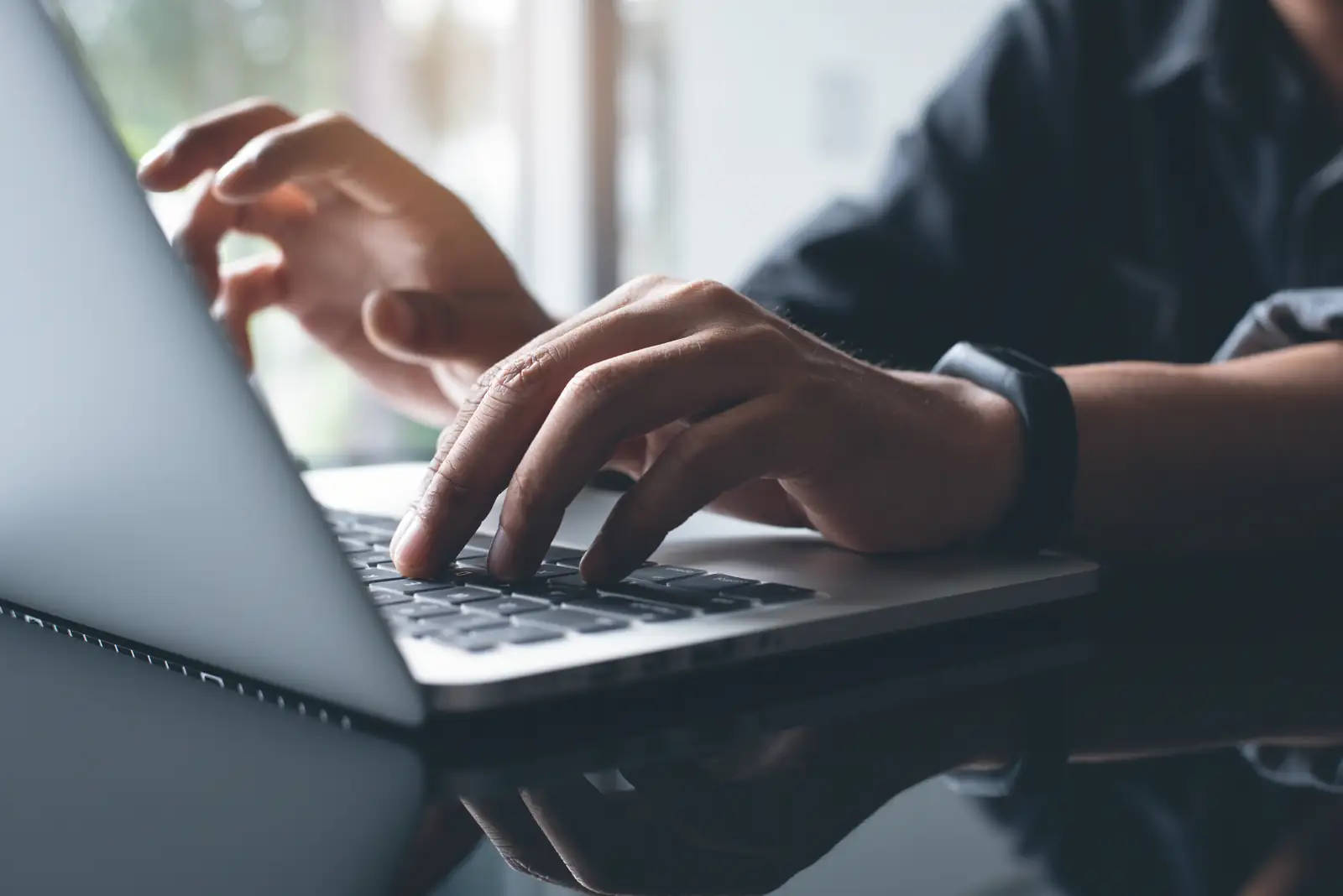
Contact us
You will be contacted by one of our experts shortly.